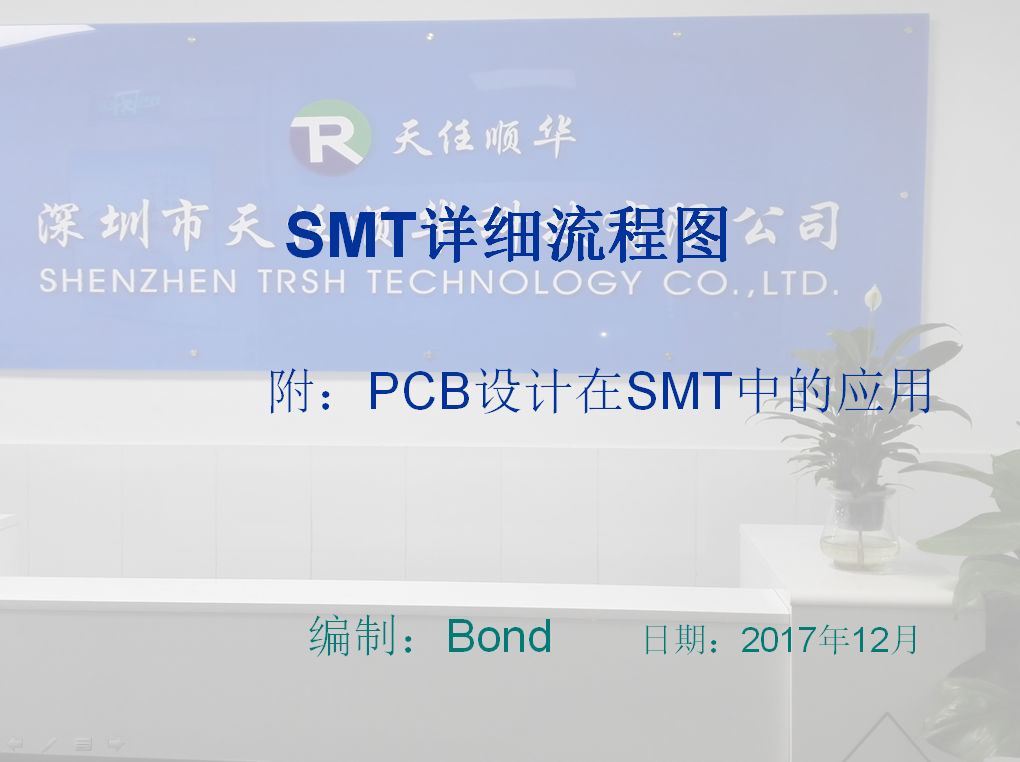
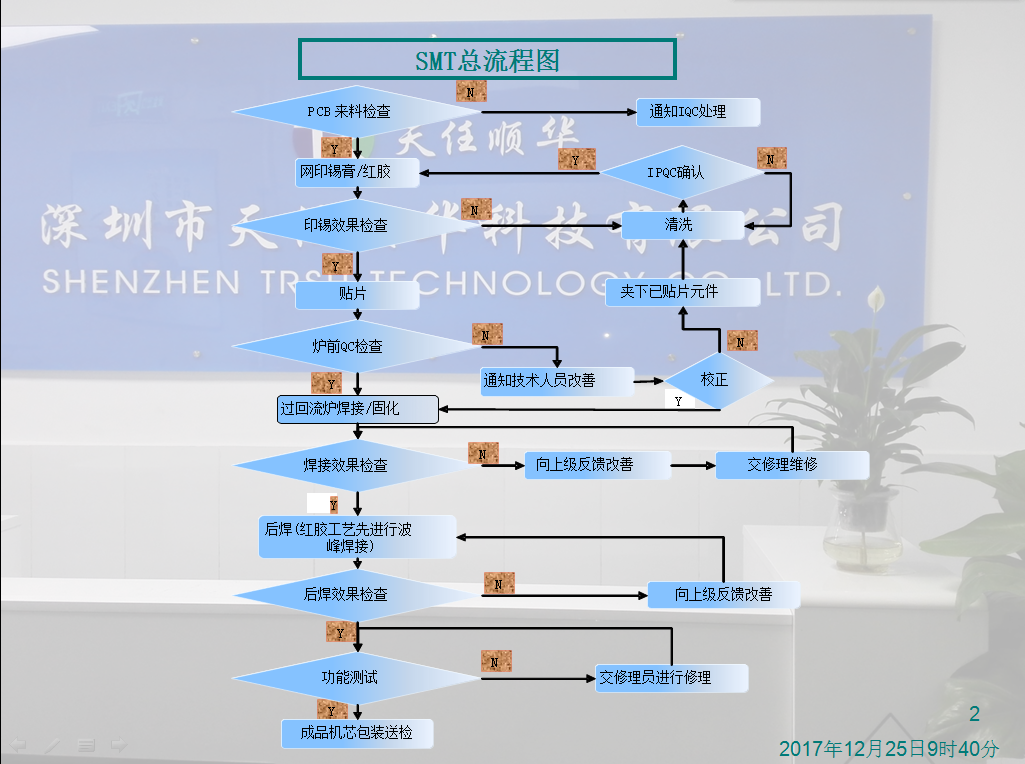

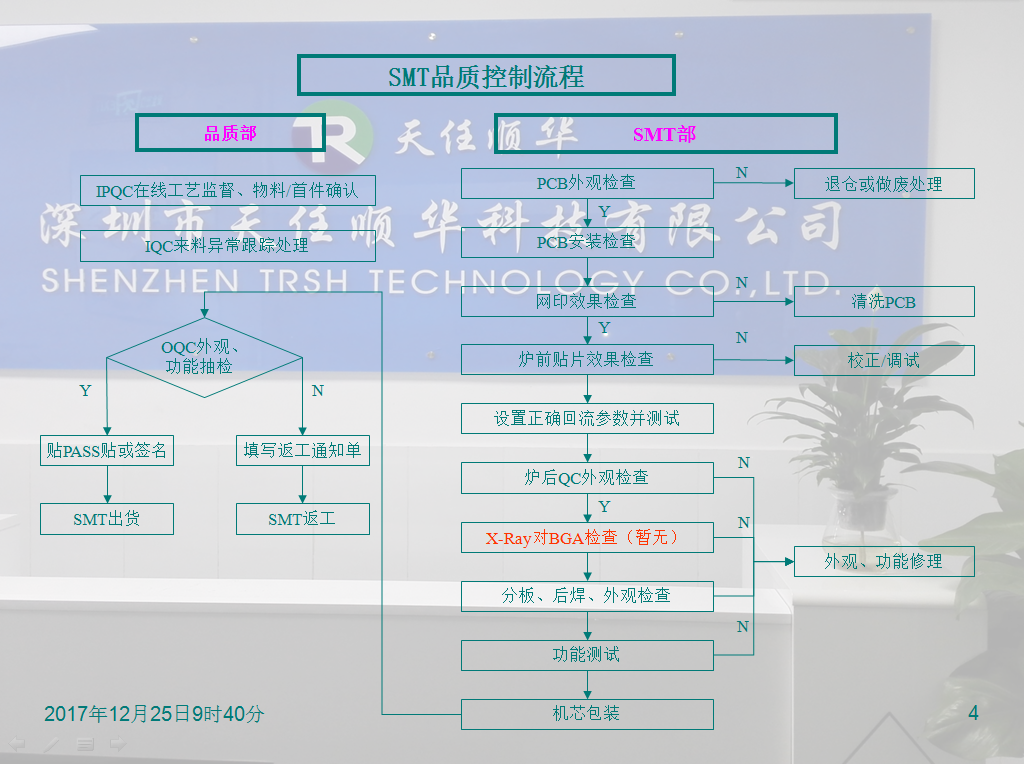
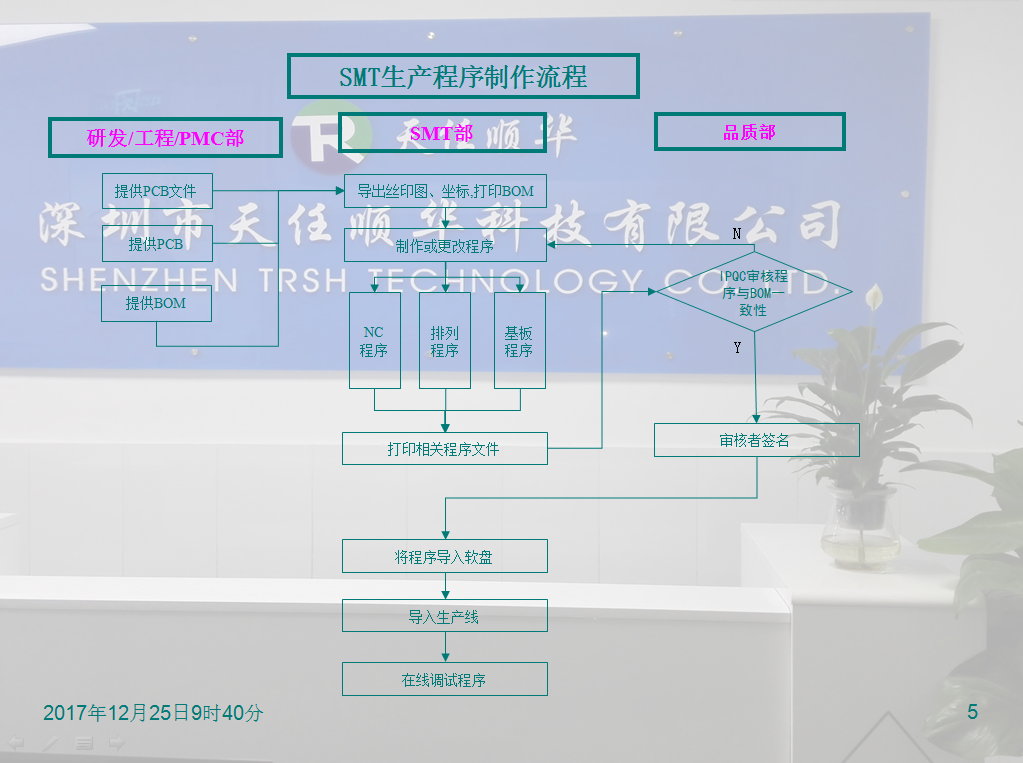

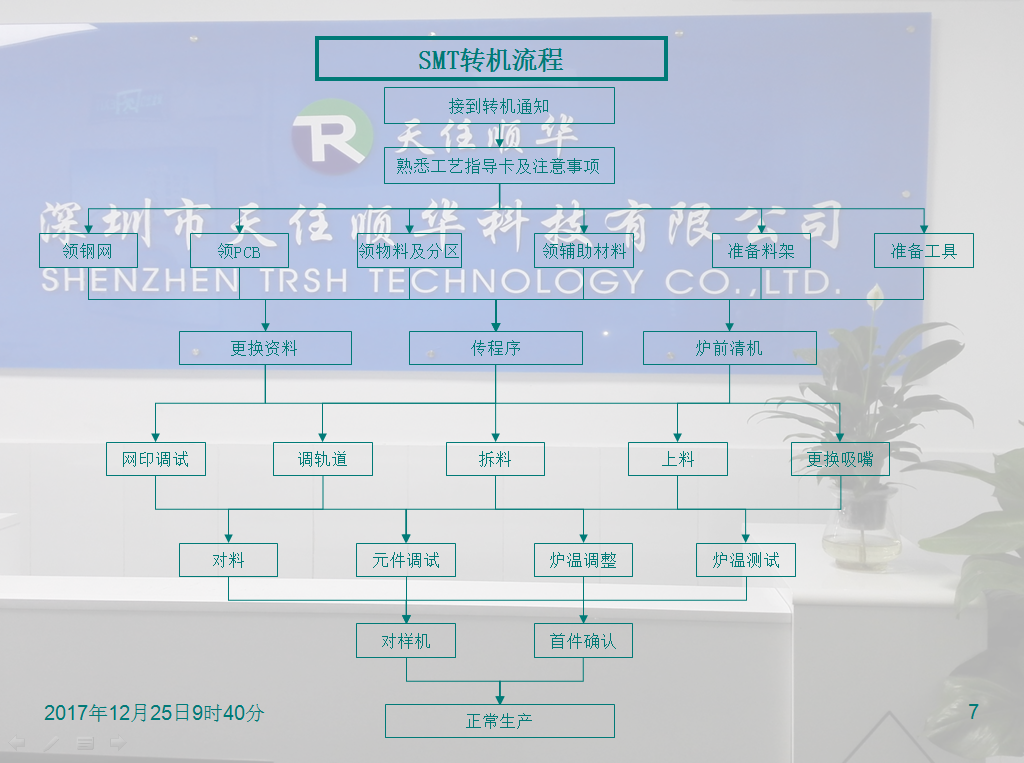
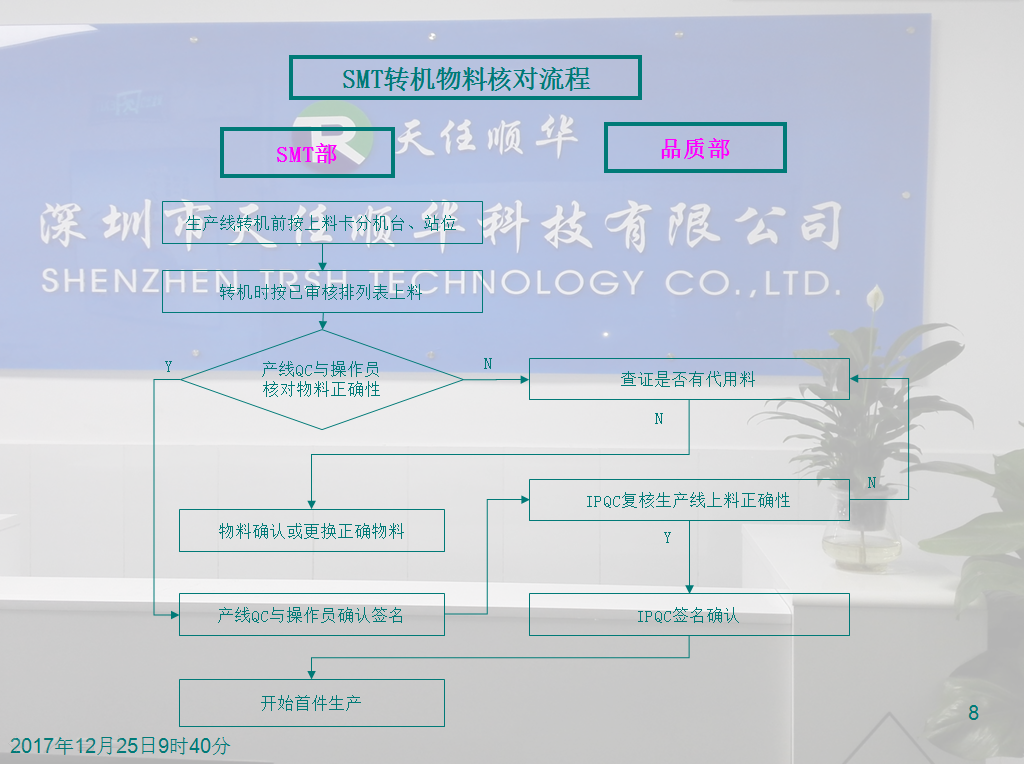
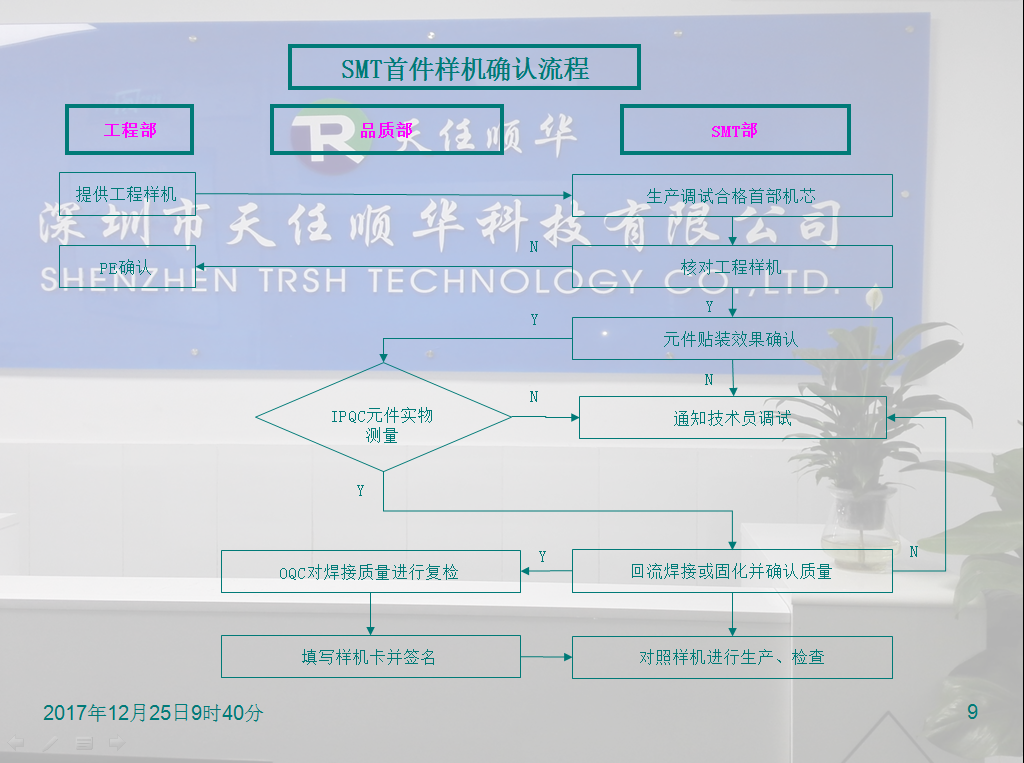
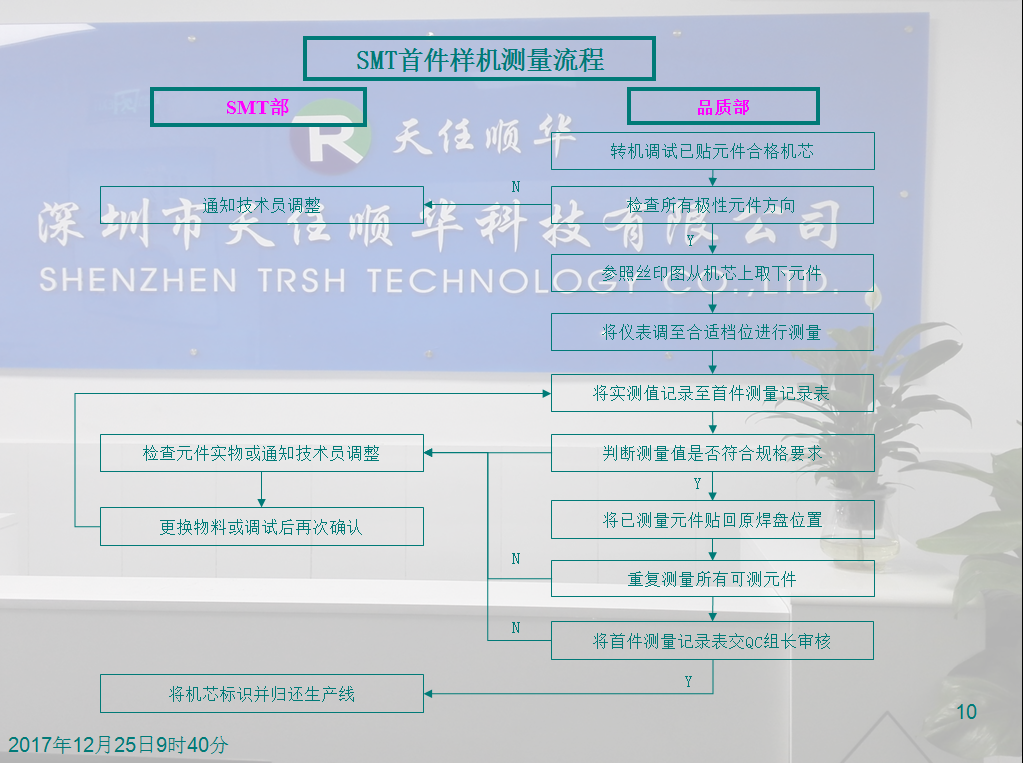


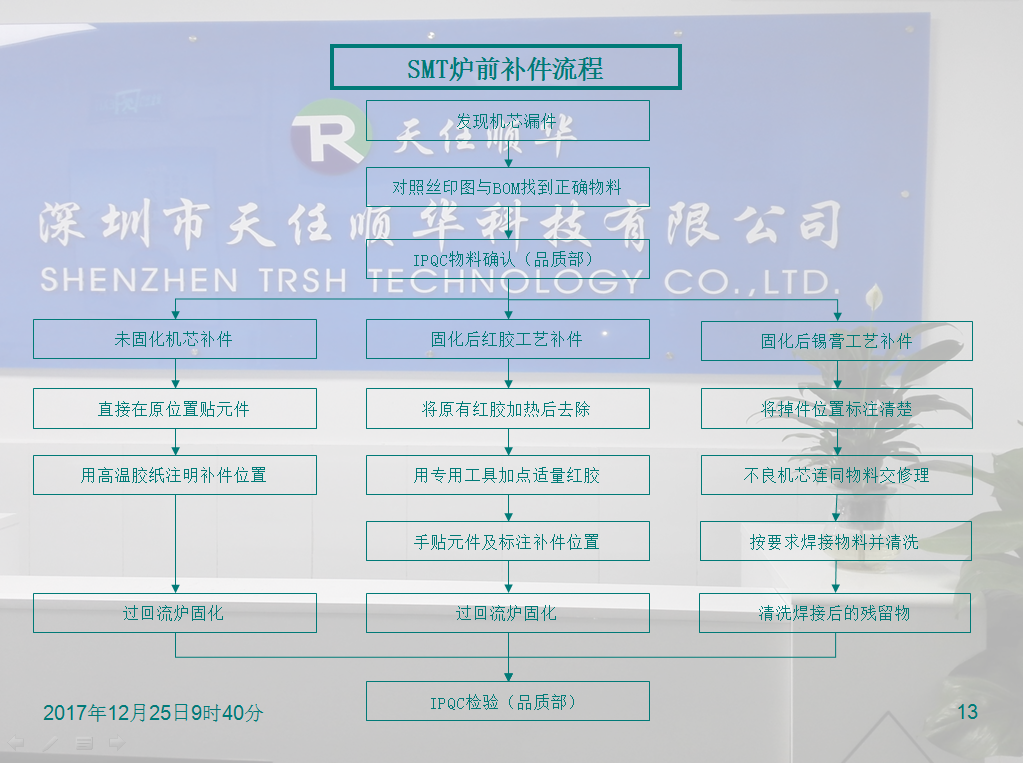
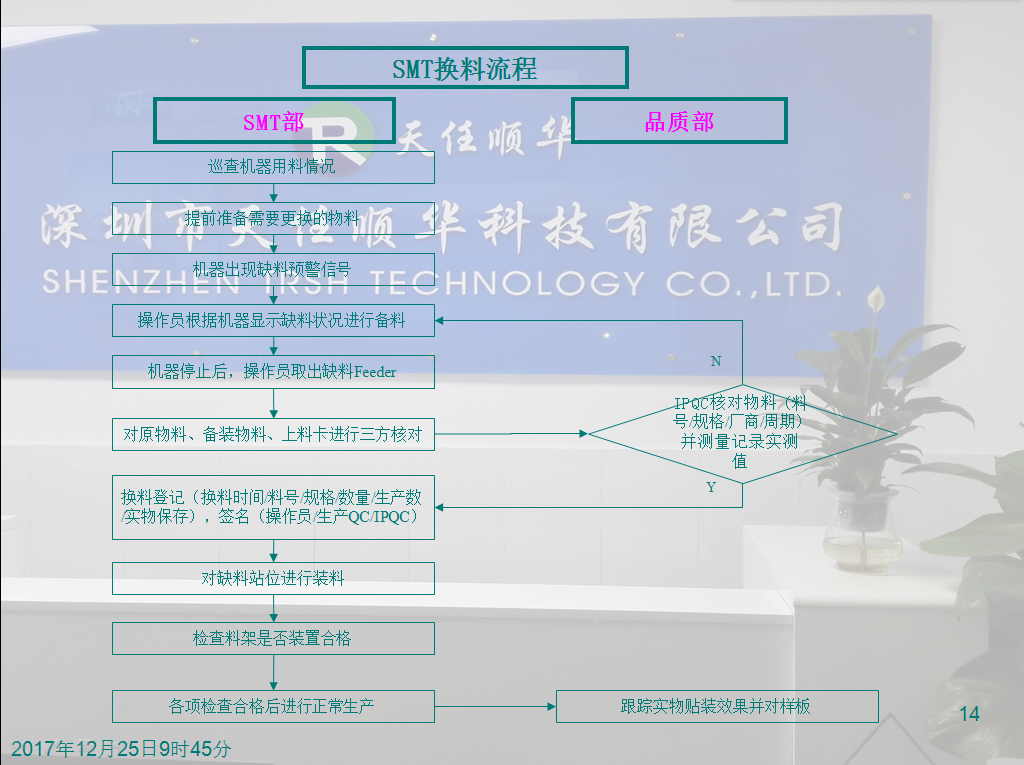
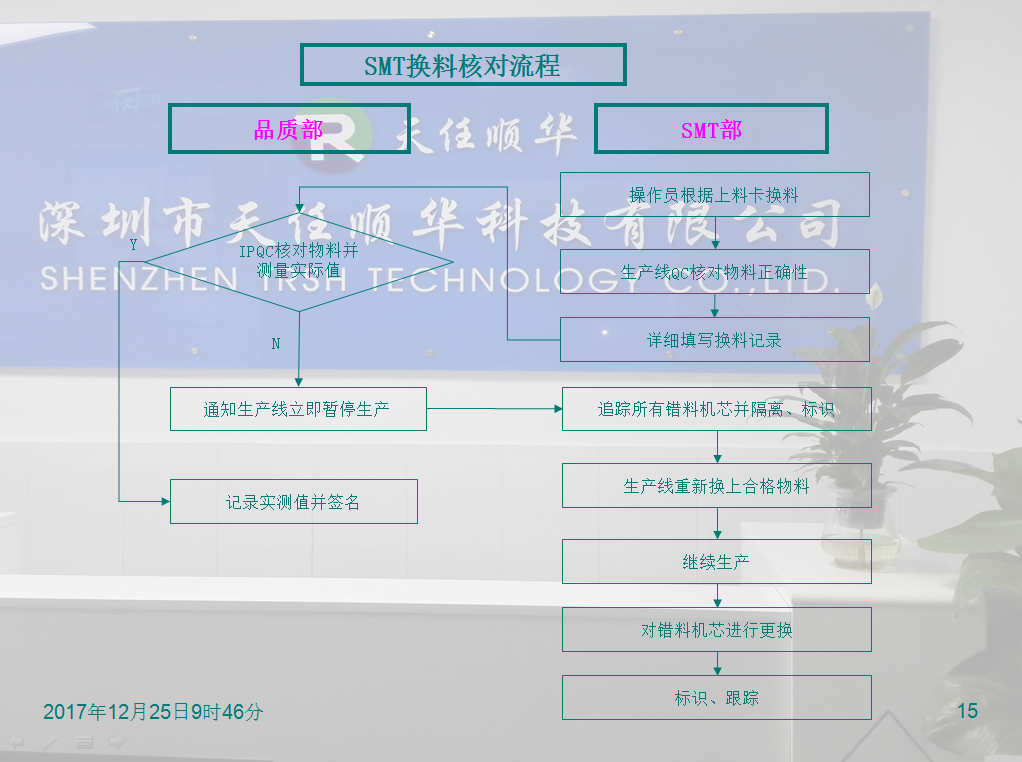
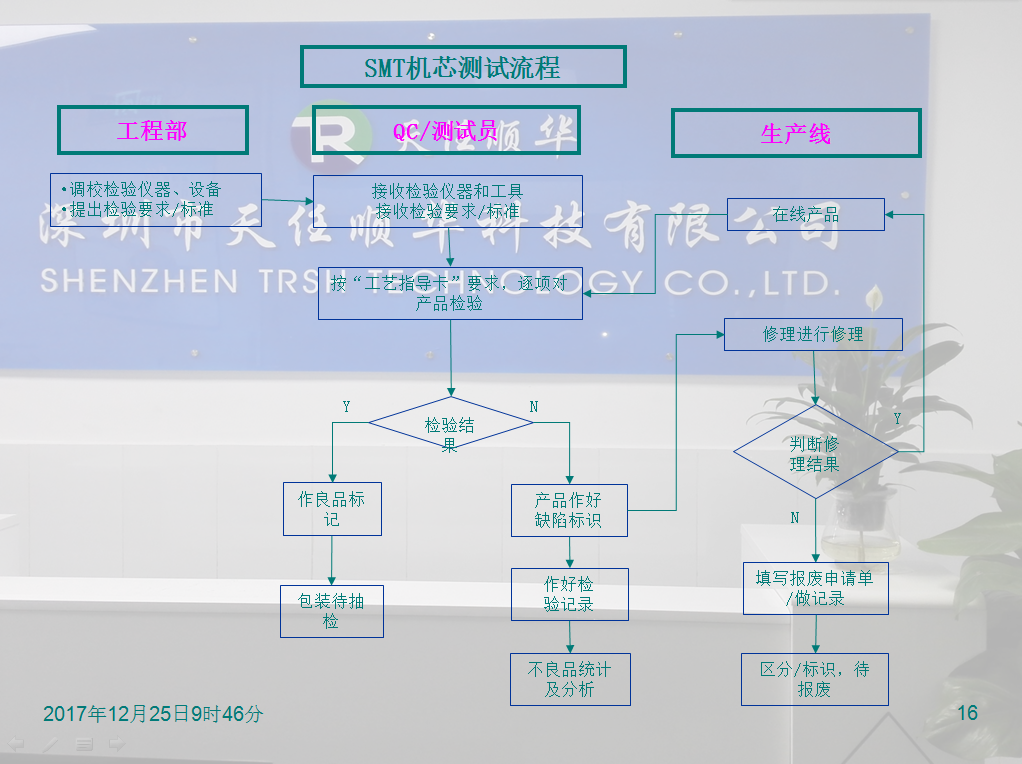
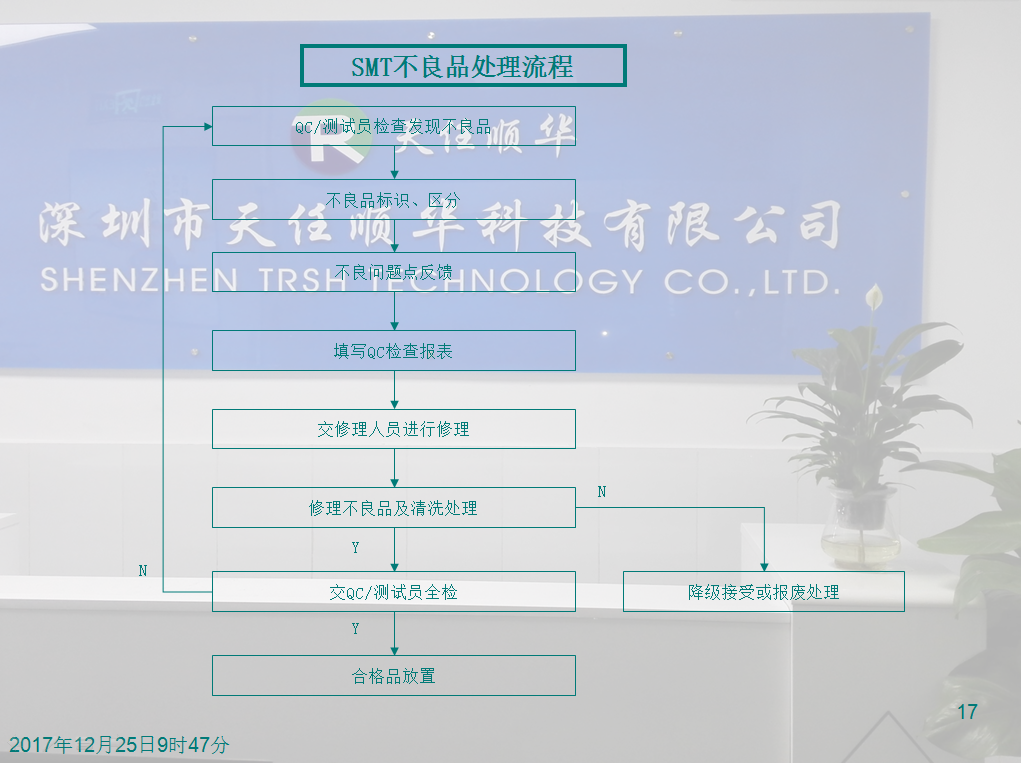

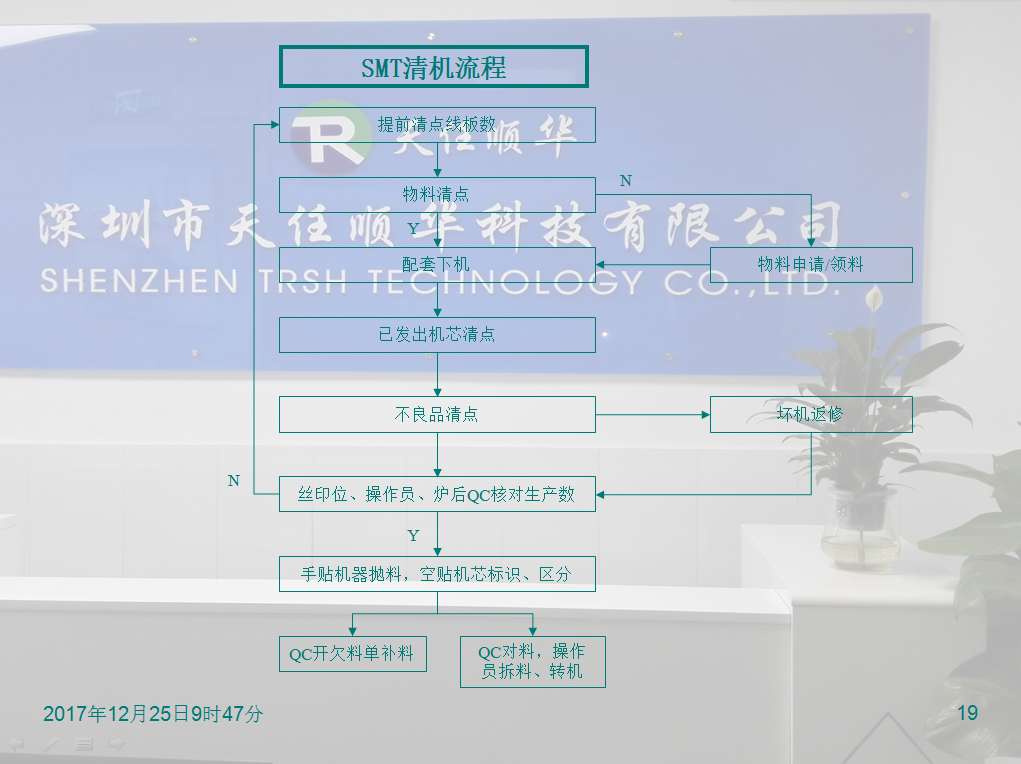
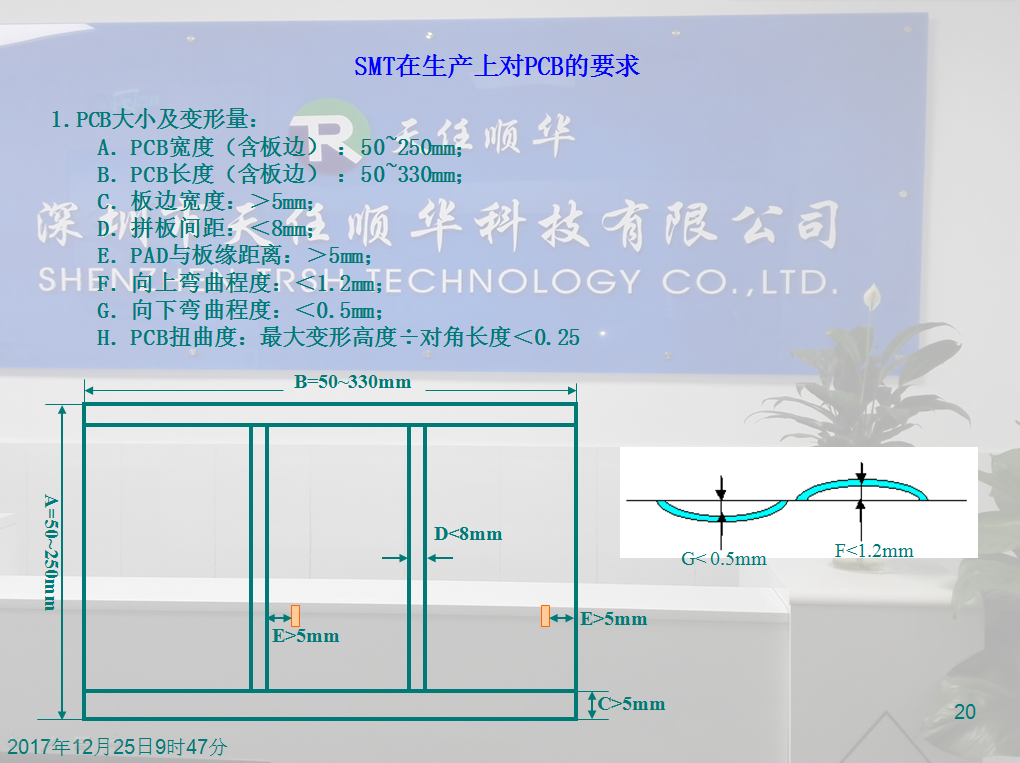

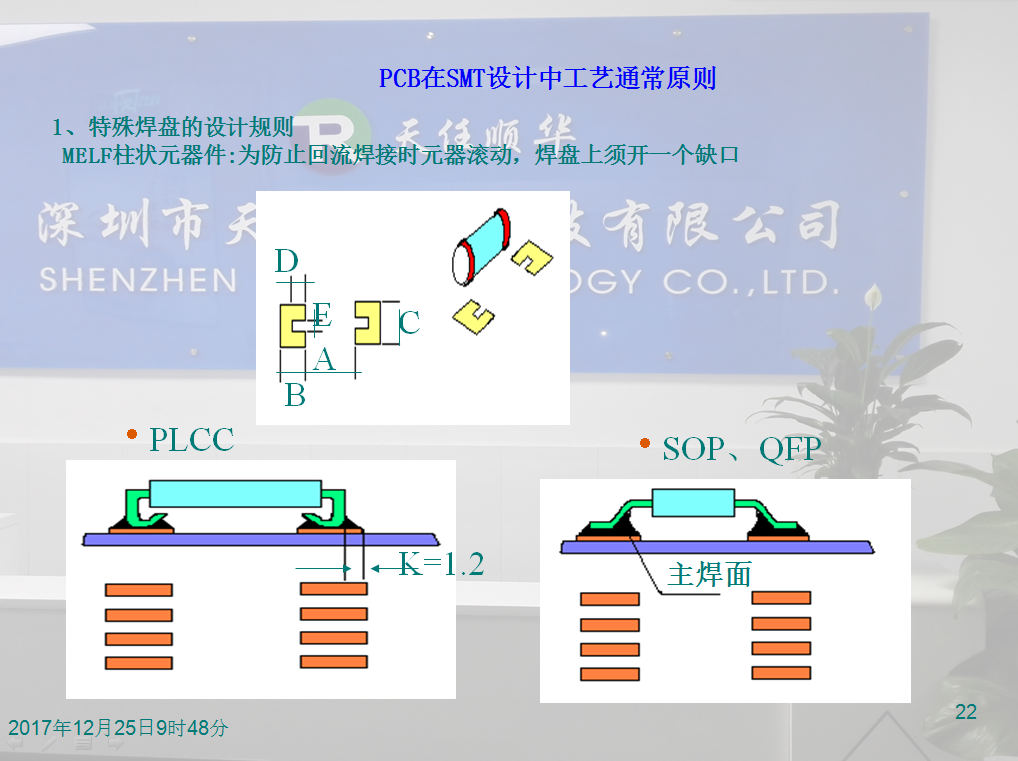

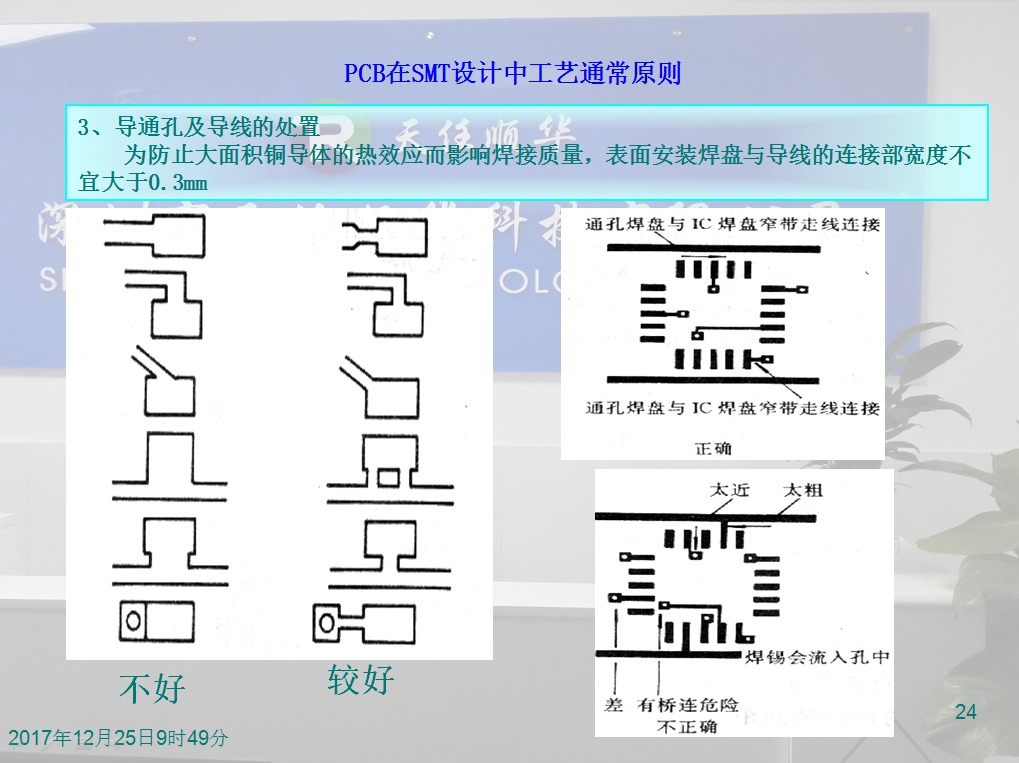
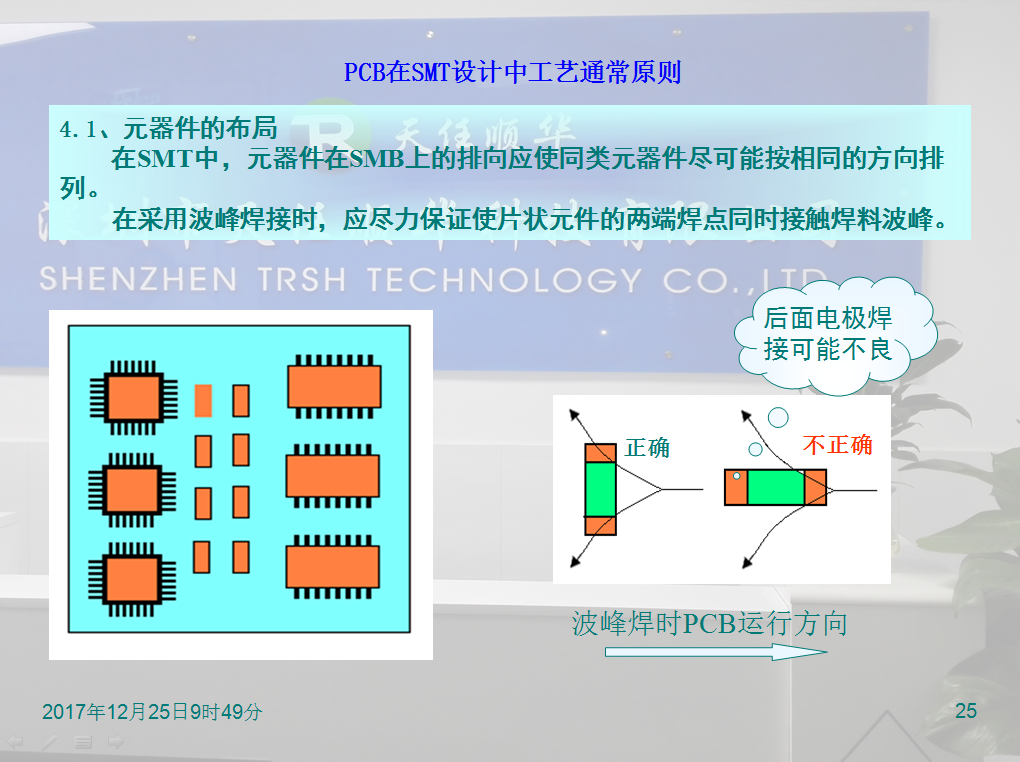

27. Introduction to SMT Terminology
1. Template: (steel mesh)
Firstly, determine whether to process the template based on the designed PCB. If the SMD components on a PCB are only resistors and capacitors, and are packaged above 1206, there is no need to make a template, and solder paste can be applied using a needle cylinder or automatic dispensing equipment; When chips containing SOT, SOP, PQFP, PLCC, and BGA packaging in the PCB, as well as resistors and capacitors with packaging below 0805, templates must be made. General templates are divided into chemically etched copper templates (with low prices, suitable for small batches, experiments, and chip pin spacing of 0.635mm); Laser etching of stainless steel templates (with high precision and price, suitable for large-scale, automatic production lines, and chip pin spacing of 0.5mm). For research and development, small batch production, or spacing of 0.5mm, it is recommended to use etched stainless steel templates; For mass production or stainless steel templates with a spacing of 0.5mm, laser cutting is used. The overall size is 370 * 470 (in mm), and the effective area is 300 * 400 (in mm).
2. Screen printing: (high-precision semi-automatic solder paste printing machine)
Its function is to use a scraper to leak solder paste or patch adhesive onto the PCB pad, preparing for the installation of components. The equipment used is a manual screen printing machine, a template, and a scraper (metal or rubber), located at the forefront of the SMT production line. It is recommended to use a medium size silk screen printing platform. The template is fixed on the screen printing platform using a precision semi-automatic screen printing machine method. The position of the PCB is determined on the screen printing platform through the up and down and left and right knobs on the manual screen printing platform, and this position is fixed; Then place the required PCB between the screen printing platform and the template, and place solder paste on the screen board (at room temperature), keeping the template parallel to the PCB. Use a scraper to evenly apply the solder paste on the PCB. During use, pay attention to timely cleaning the template with alcohol to prevent solder paste from blocking the leakage holes of the template.
3. Placement: (Korean high-precision fully automatic multifunctional placement machine)
Its function is to accurately install surface mount components onto the fixed position of the PCB. The equipment used is a mounting machine (automatic, semi-automatic or manual), vacuum suction pen or tweezers, located behind the silk printing table in the SMT production line. For laboratories or small batches, it is generally recommended to use double headed anti-static vacuum suction pens. To solve the installation and alignment problems of high-precision chips (with a pin spacing of 0.5mm), it is recommended to use the Samsung fully automatic multifunctional high-precision placement machine (model SM421 can improve efficiency and installation accuracy) from South Korea. The vacuum suction pen can directly pick up resistors, capacitors, and chips from the component rack. Due to the adhesive nature of the solder paste, resistors and capacitors can be directly placed in the desired position; For chips, a suction cup can be added to the vacuum pen tip, and the suction force can be adjusted through a knob. Remember to align the components regardless of their placement. If they are misaligned, the PCB must be cleaned with alcohol, re screen printed, and the components must be repositioned.
4. Reflow soldering:
Its function is to melt the solder paste, firmly braze the surface mounted components with the PCB to achieve the electrical performance required by the design, and precisely control it according to international standard curves, effectively preventing thermal damage and deformation of the PCB and components. The equipment used is a reflow soldering furnace (fully automatic infrared hot air reflow soldering furnace), located behind the SMT production line SMT placement machine.
5. Cleaning:
Its function is to remove substances or welding residues such as soldering flux that affect the electrical performance of the mounted PCB. If cleaning free solder is used, it is generally not necessary to clean it. For products that require low power consumption or good high-frequency characteristics, cleaning should be carried out. Generally, products can be cleaned free. The equipment used is an ultrasonic cleaning machine or manually cleaned with alcohol, and the position may not be fixed.
6. Inspection:
Its function is to inspect the welding quality and assembly quality of the assembled PCB. The equipment used includes magnifying glasses and microscopes, which can be configured at suitable locations on the production line according to the inspection needs.
7. Repair:
Its function is to rework the PCB that has detected faults, such as solder balls, solder bridges, open circuits, and other defects. The tools used are intelligent soldering irons, repair workstations, etc. Configured anywhere in the production line.
4、 SMT auxiliary process: mainly used to solve mixed processes of wave soldering and reflow soldering.
1. Red glue printing: (can also print red glue)
The function is to apply red offset printing to the fixed position of the PCB, mainly to fix the components onto the PCB. It is generally used for surface mount components on both sides of the PCB and wave soldering on one side. The equipment used is a printing machine for solder paste and red glue printing, which can be completed by one machine and is located at the forefront of the SMT production line.
2. Curing: (Reflow soldering is better for curing and with lead solder paste)
Its function is to solidify the patch adhesive under heat, thereby firmly bonding surface mounted components and PCBs together. The equipment used is a curing furnace (the reflow soldering furnace can also be used for adhesive curing and thermal aging testing of components and PCBs), located behind the SMT production line's SMT mounting machine.
Conclusion:
SMT surface mounting technology includes many aspects, such as the design and manufacturing technology of electronic components and integrated circuits, circuit design technology of electronic products, design and manufacturing technology of automatic mounting equipment, development and production technology of auxiliary materials used in assembly and manufacturing, anti-static technology of electronic products, etc. Therefore, the production of a complete, beautiful, and well tested electronic product will be influenced by many factors.
